6 Common Pitfalls to Avoid with Virtual Commissioning
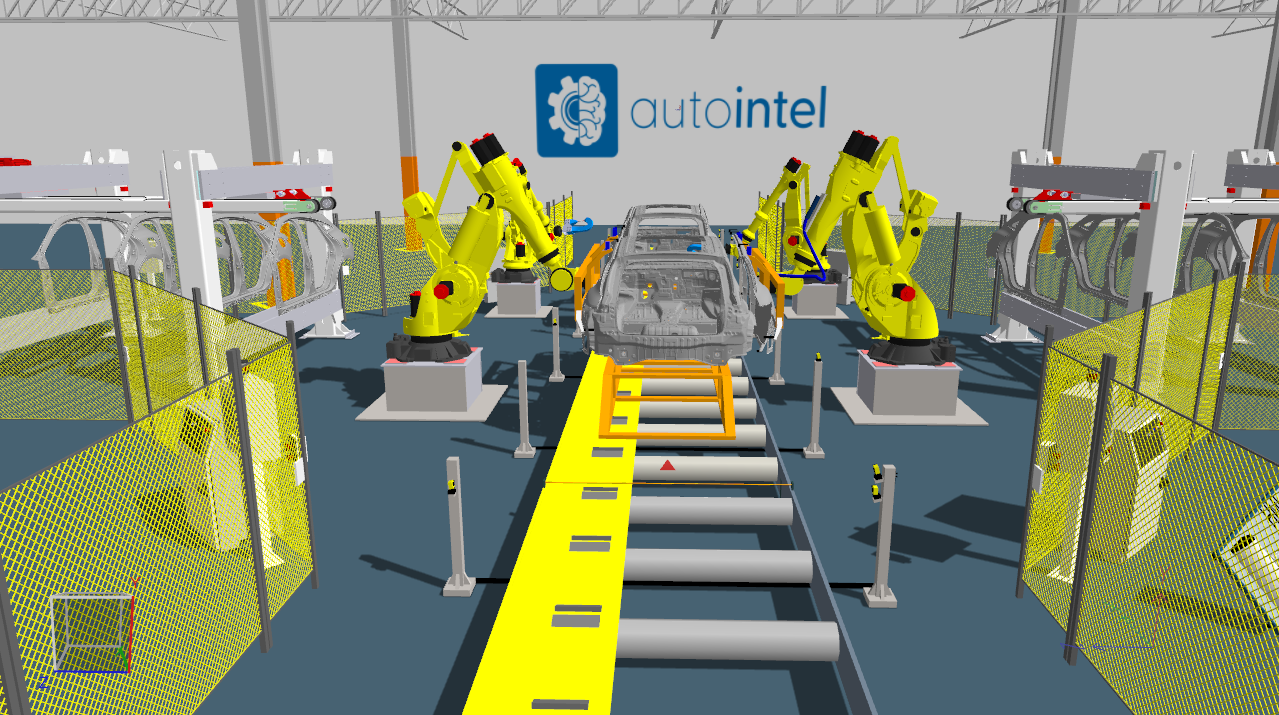
This post is part of a month-long series dedicated to Virtual Commissioning. You can also download our free Virtual Commissioning Playbook here for more details on the process and benefits of VC.
Virtual commissioning has transformed the way industries implement automation systems by providing a simulated environment to test and validate control systems before they go live. This process saves time, reduces costs, and minimizes risks by identifying potential issues early.
However, common pitfalls can compromise its effectiveness and result in costly mistakes.
In this blog post, we'll explore the six most common pitfalls that manufacturers encounter during virtual commissioning (VC). By understanding and avoiding these pitfalls, you can ensure a smoother and more successful VC process, ultimately leading to a more efficient and reliable manufacturing system.
1. Stakeholder Misalignment
Stakeholder misalignment in a VC process can manifest in several ways, disrupting the project's flow and leading to inefficiencies or even failure. To avoid these challenges, it’s important to start the process by establishing clear communication channels, aligning objectives, setting realistic expectations, and ensuring that all stakeholders are educated about the VC process and its benefits. This includes internal stakeholders of your manufacturing company as well as your OEM and virtual consulting partners. Regular meetings and updates can help keep everyone on the same page and facilitate smoother collaboration.
2. Resource Scheduling & Capacity
Under the same umbrella as stakeholder misalignment, a critical part of any VC project is making sure that the team is aligned on the dedicated resources needed to keep execution on schedule. In addition to providing code a little earlier in the process, your controls engineers will need to be available and engaged during debug and testing on the virtual equipment. Not only is that helpful to you, the manufacturer, but also the more the team is engaged in VC, the more they will benefit from a faster startup on the factory floor as well.
3. Inexperienced Consultants
Ensuring you have the right team of virtual engineering consultants with robust controls experience is critical to the success of a VC project. Experienced engineers bring a deep understanding of both the software and hardware aspects of automation. This enables them to adeptly navigate the complexities of creating accurate models, integrating various system components, and identifying potential issues early in the process.
4. Misalignment Between Virtual and Physical Systems
Once VC model development begins, the electrical and mechanical designs at that moment are handed off to the VC team. As the project progresses through design reviews and eventual build, these designs may evolve. To prevent discrepancies between the virtual model and the physical equipment, it is crucial to maintain close coordination with the VC team to integrate these updates. Without this synchronization, the team might fully program and test the virtual equipment, only to encounter new bugs during physical installation due to uncommunicated changes in components or functionality.
5. Overlapping Physical and Virtual Commissioning
To get the most value out of VC, the testing and debug phase needs to be executed prior to the start of physical commissioning. Completing a thorough VC process is what will reduce time spent in the field and minimize impacts to production. If the schedule slips and VC winds up happening simultaneously with physical commissioning, it causes resource constraints and dilutes the effectiveness of the VC process.
6. Early Integration of Multiple Models
It’s not uncommon that while performing VC for one subsystem, end users might envision a full production site scale model that contains all of the various subsystems and machinery in a single virtual environment. Sometimes this is appropriate, but if it’s done too early in the project, often it only ties the schedules and test availability of the subsystems together. In that case, a design change or delay to one subsystem would now impact the model that houses all of your systems. Maintenance events would also impact the ability to parallelize software development and test. Whenever possible, it’s best to execute VC models and virtual startups at the lowest unit of control possible and plan for integration efforts to occur later in the process.
How can we help you avoid these pitfalls?
Virtual commissioning, while transformative, is not without its challenges. By being aware of and avoiding these six common pitfalls discussed, you can significantly enhance the success rate of your virtual commissioning projects. Adequate planning, effective communication, and guaranteeing you have the right expertise are all important components that can make or break your project.
If you find yourself in need of expert guidance, consider partnering with Automation Intelligence. Our team of experienced professionals is dedicated to helping you streamline your virtual commissioning process, avoid common pitfalls, and achieve optimal results.
Headquarters
We have a team of engineers positioned across the US, but our primary HQ is in Atlanta, GA.