Digital Twins: Increasing Profits and Productivity with a Virtual Replica
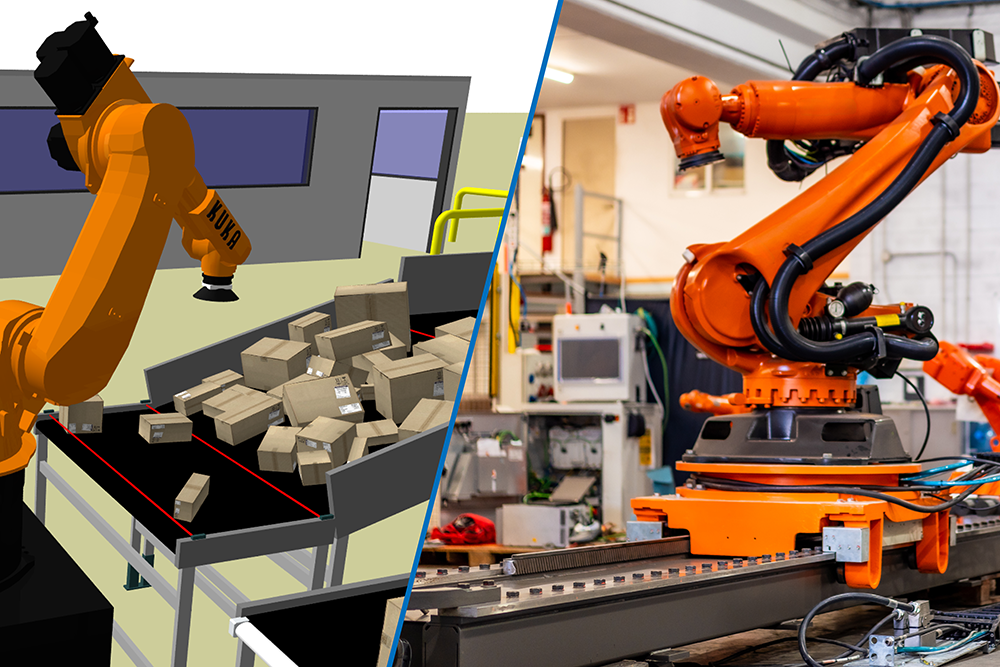
What is a digital twin?
Have you ever walked the floor of your plant, or stood on a catwalk observing operations below, and found yourself wondering if a few changes to your production cycle could make a big impact?
Could that line be sped up?
Could you change your SKU mix to reduce changeovers?
Can you handle demand during peak season?
Before making major financial and time commitments to overhaul your facility, you can definitively answer those questions with a digital twin.
Digital twin models are dynamic, virtual representations of physical manufacturing assets, such as equipment, production lines, and even entire factories. They are physics-enabled, temperature-sensitive, and can utilize the same PLC code as the actual factory equipment. They function exactly the same as the real-life version of a production system, which allows company stakeholders to test different scenarios, gather data, and analyze the best return on investment options to improve business efficiency and success.
How are digital twins built?
Digital twins are built using a combination of CAD (Computer-Aided Design) models, sensor data, historical performance data, and real-time operational data. By capturing and integrating this wealth of information, digital twins provide a comprehensive view of a factory or warehouse’s operations, enabling business leaders to monitor, analyze, and optimize operations in real-time.
How does Automation Intelligence utilize digital twin technology?
Digital twin models can be used to serve multiple purposes. At Automation Intelligence, we specialize in utilizing them for virtual commissioning, as well as emulation and simulation consulting.
Virtual commissioning is a methodology used in manufacturing and engineering industries to test and validate control systems and processes in a virtual environment before physical implementation. In this case, a digital twin allows us to assess various scenarios, control strategies, and operational sequences to ensure that the system operates as intended and meets performance requirements. This proactive approach helps minimize downtime, reduce maintenance costs, and extend the lifespan of assets.
By leveraging advanced analytics and machine learning algorithms, digital twin models can also optimize production schedules, resource allocation, and inventory management; helping manufacturers achieve higher levels of productivity and agility while maintaining quality standards.
Cloud-hosted models: Making the most of a digital twin
One unique aspect of AutoIntel’s digital twin consulting services is that we offer our clients the opportunity to continue utilizing their model after the initial consulting project concludes. Clients can access their digital twin via our cloud-hosted platform, where they can continue to analyze production runs, make modifications, and test other scenarios.
Digital twins are an innovative way to improve operations
Overall, digital twin models play a crucial role in driving innovation and competitiveness in many industries including retail and eCommerce, warehouse logistics, and consumer goods manufacturing. By providing actionable insights and enabling data-driven decision-making, digital twins can help resolve challenges and improve business efficiency at every stage of the production lifecycle.
Headquarters
We have a team of engineers positioned across the US, but our primary HQ is in Atlanta, GA.