How Can Simulation Improve an Automated Storage and Retrieval System?
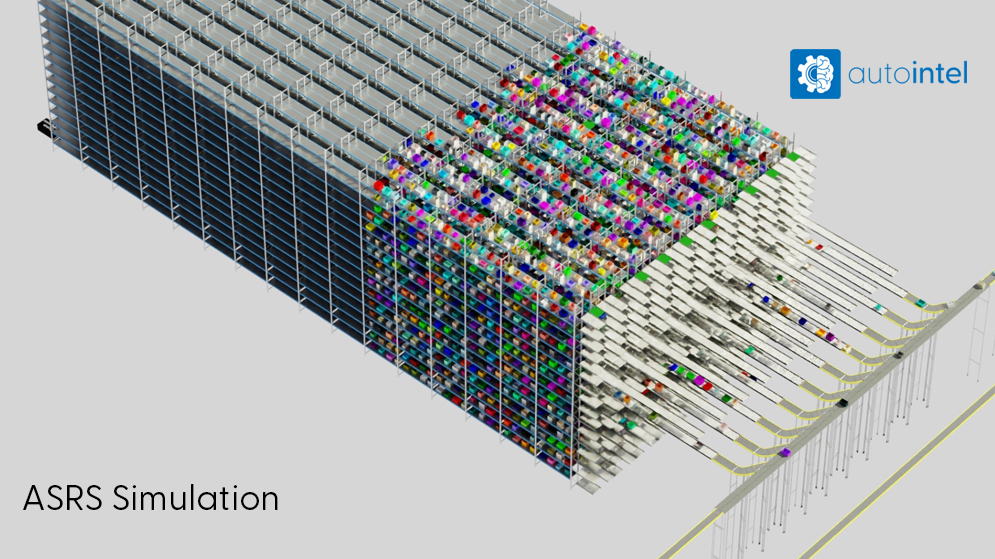
Automated storage and retrieval systems (ASRS) play a key role in modern order fulfillment centers. They help manage order buffering between waves and store items for the downstream operators who pack the orders.
When you're updating an existing facility or planning a new one, it's crucial to make sure these systems can efficiently move products in and out without disrupting other operations.
Using simulation modeling can be very useful here. It lets you see how all the complex systems work together and quickly test various scenarios to make sure everything is the right size and fit for the operations.
Such scenarios could include:
- Peak Season vs. Average Day
- Today's Volume vs. Future Volume
- What-if Scenarios (e.g. what if part of a system goes down temporarily?)
- Changing Order Profiles (five lines per order vs. ten)
When evaluating scenarios over time, we collect and assess various points, including total system storage over time, wait time for entry and exit, shuttle and elevator utilization, and conveyor traffic and utilization.
In the case of automated buffer systems, our detailed modeling and analysis typically includes:
- Total storage capacity
- Shuttle systems (acceleration, deceleration, max speed)
- Contamination constraints (such as food contaminants stored on top of other like products)
- Elevator systems (acceleration, deceleration, max speed)
- Traffic into and out of the cells
- Sequence and algorithm for push/pull into and out of the cells
- Conveyor and sorter capacity into and out of the system.
During our analyses, it’s not uncommon for us to uncover issues with the system design. Simulation allows us the ability to quickly reconfigure the design parameters with your team in order to resolve these issues.
Automated storage systems are typically a significant line item of the project budget and carry a high risk for effective system performance. Simulation allows for the most detailed analysis of these components and ensures they're properly sized and designed for current and future peak needs. This allows the consumer of these systems to ensure their investment is right-sized and avoids costly design changes later in the CapEx process.
Headquarters
We have a team of engineers positioned across the US, but our primary HQ is in Atlanta, GA.