How to use Simulation Modeling to Right-Size an Autonomous Vehicle Fleet
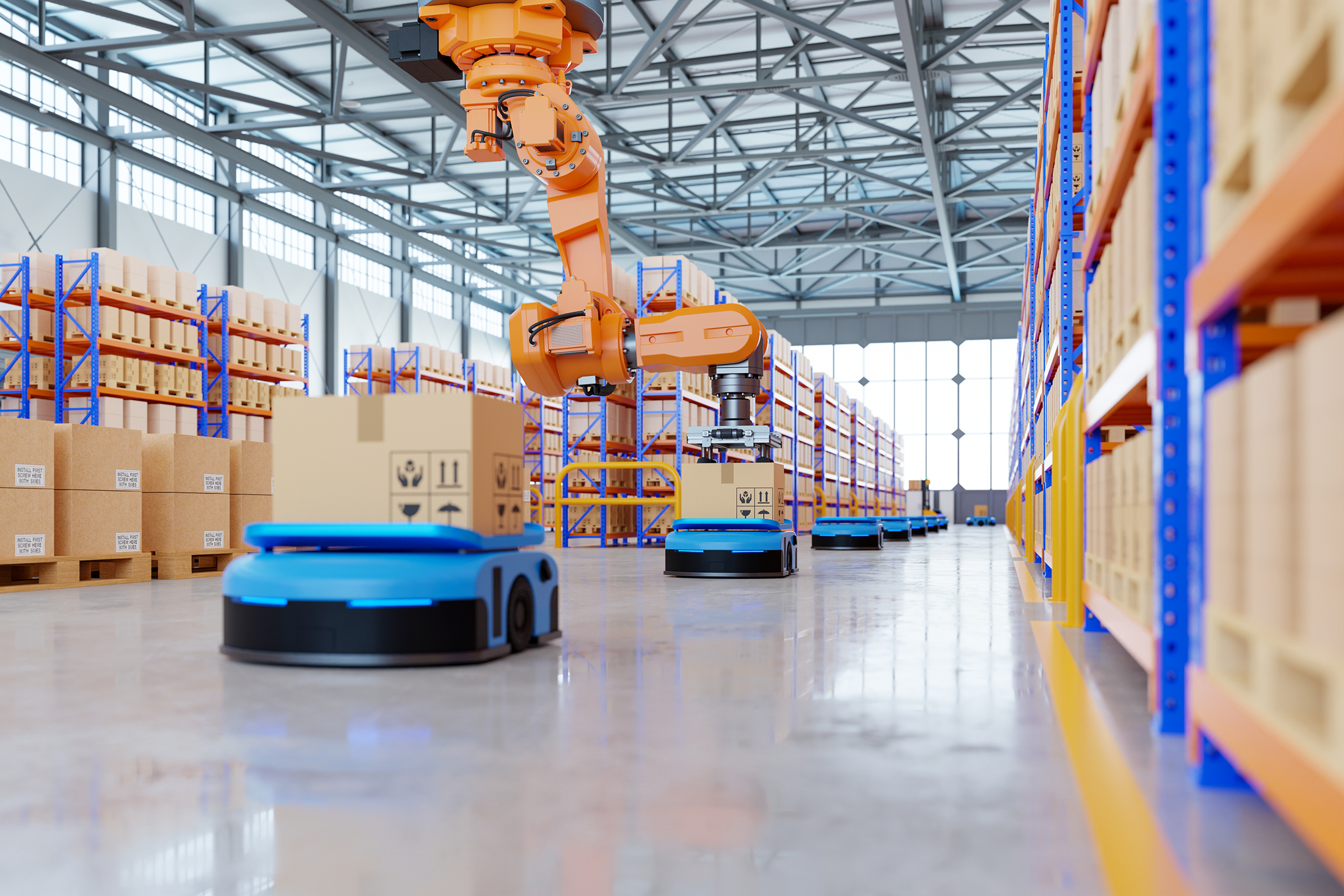
When it comes to warehouse logistics, ensuring that your autonomous guided vehicle (AGV) fleet is perfectly sized to meet operational demands without incurring unnecessary costs is crucial. Simulation modeling is a powerful ally in this endeavor, offering a cost-effective approach to fleet optimization.
By recreating the behavior of daily production in a simulated model, you can assess the natural ebbs and flows of your AGV pool. You can also experiment with different fleet configurations (for example, bifurcating or zoning certain areas of your facility), forecast potential issues, and predict outcomes. This enables you to make informed decisions about the number and type of AGVs required, ensuring efficient and cost-effective operations.
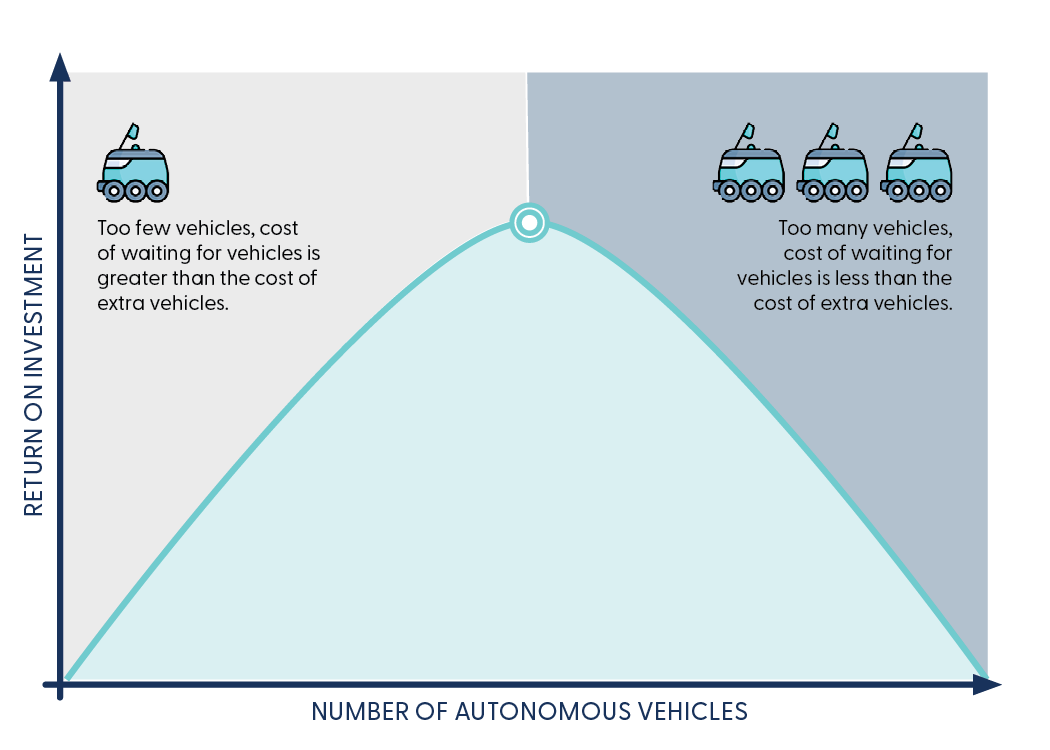
In this blog post, we explore how our simulation consulting services can help right-size your AGV fleet, driving both productivity and profitability.
Simulation modeling begins with gathering accurate inputs
To simulate your operations and current AGV fleet usage, we have to begin by gathering some critical data points. Here are a few things we’ll need to know:
- AGV Motion Profile: What are the accurate parameters for your AGV’s acceleration, deceleration, max speed when unloaded, and max speed when loaded.
- Battery Life: What is the battery capacity for each AGV and its depletion rate?
- Charging Plans: How often do you charge each AGV and where are the charger locations within your facility?
- Blueprints & Paths: How is your facility laid out and where are the designated travel paths for the AGVs?
- Profiles & Logic: What type of information do you utilize for each order profile and what is the dispatch logic for sending an AGV to fulfill an order? Also, what is the logic for how a a specific AGV is selected?
It’s important to note that while some of this data collection and analysis can be completed with a spreadsheet, that’s not the best way to see the whole picture. Spreadsheets can miss critical impacts like traffic, congestion, and other important minute-to-minute details.
Our process for simulation modeling and data analysis
Once we have the critical inputs gathered, we will begin our process of creating the simulation model, validating the systems and logic, and analyzing the outcomes.
Layout & Vehicle Configuration
The first step in right-sizing your autonomous vehicle fleet using simulation modeling involves recreating your warehouse layout, including all pick-up and drop-off locations. This detailed digital replica serves as the foundation for accurately recreating the movement of vehicles within your facility. Once the layout is established, it's crucial to create the travel paths that these vehicles will follow. This step ensures that the simulation accurately reflects the real-world routes and potential bottlenecks vehicles may encounter during operations.
Configuring Algorithms & Input Data
With the layout and travel paths in place, the next phase involves connecting the order profiles and sequencing logic. This means integrating data about the types and frequencies of orders your warehouse processes, as well as the logical sequence in which tasks are completed. Developing the assignment logic is another critical component, as it determines how tasks are distributed among the autonomous vehicles. This configuration allows the simulation to model the decision-making processes that occur during actual operations.
Validation
Next, it’s essential to validate that the simulation accurately represents reality. This involves comparing the model's output with real-world data to ensure it faithfully replicates the behavior of your warehouse operations. An accurate model is crucial for making reliable predictions and informed decisions about fleet sizing and management.
Analysis
Once validated, the simulation can be used to test various levels of autonomous vehicle deployment over a typical 1-5 day period. During this phase, it’s important to analyze key performance indicators (KPIs) such as blocked time, location, idle time, and waiting time for pick-ups.
Continuing this testing and analysis across various future growth scenarios and order profiles is essential. It may also be necessary to explore potential changes to travel paths and layout configurations to accommodate evolving operational needs.
This analysis will help you identify inefficiencies and areas for improvement including (but not limited to):
- Optimal investment cliffs for expanding your AGV fleet size based on future demand.
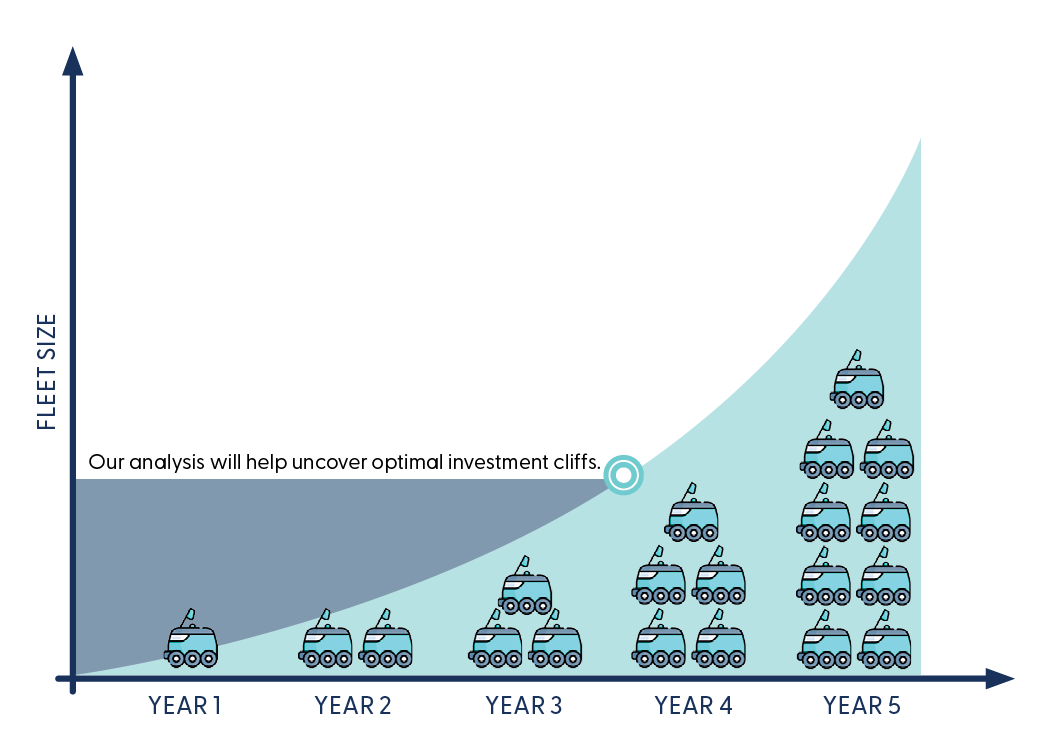
- Per minute costs of waiting for an AGV, which will allow you to do an accurate cost comparison between sizing your fleet to meet peak demand (knowing this will mean many AGVs go unused during slower cycles) versus sizing your fleet to meet average demand (knowing this will mean longer wait times during peak cycles).
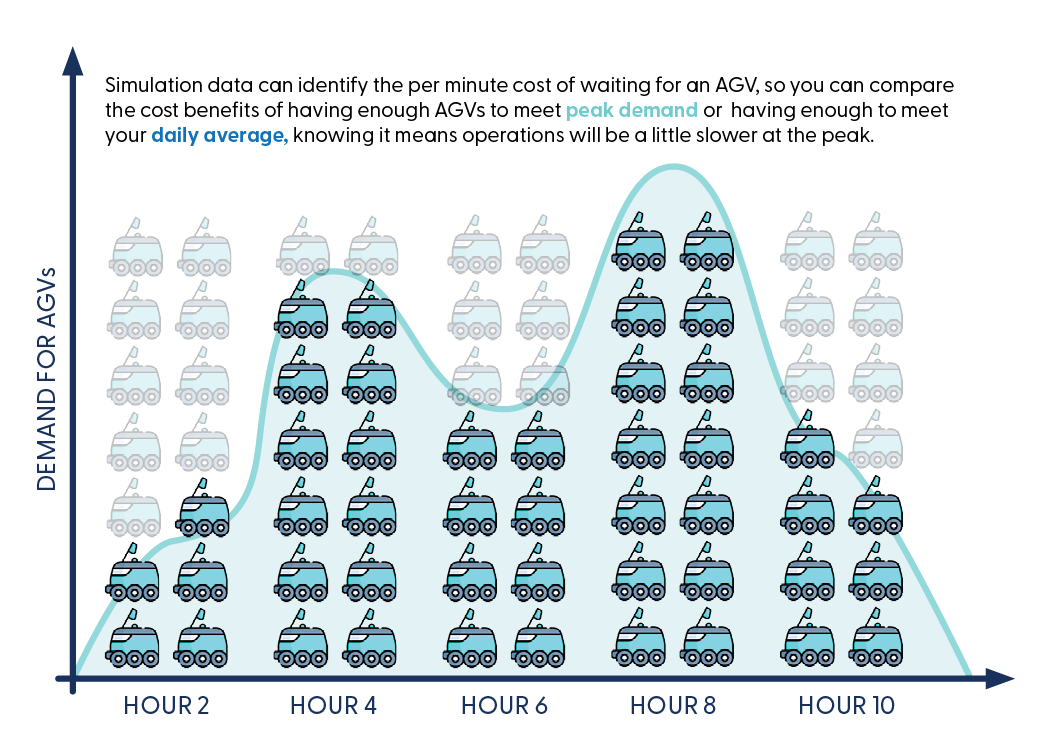
- The point at which you’ll reach a diminishing return on future AGV investments.
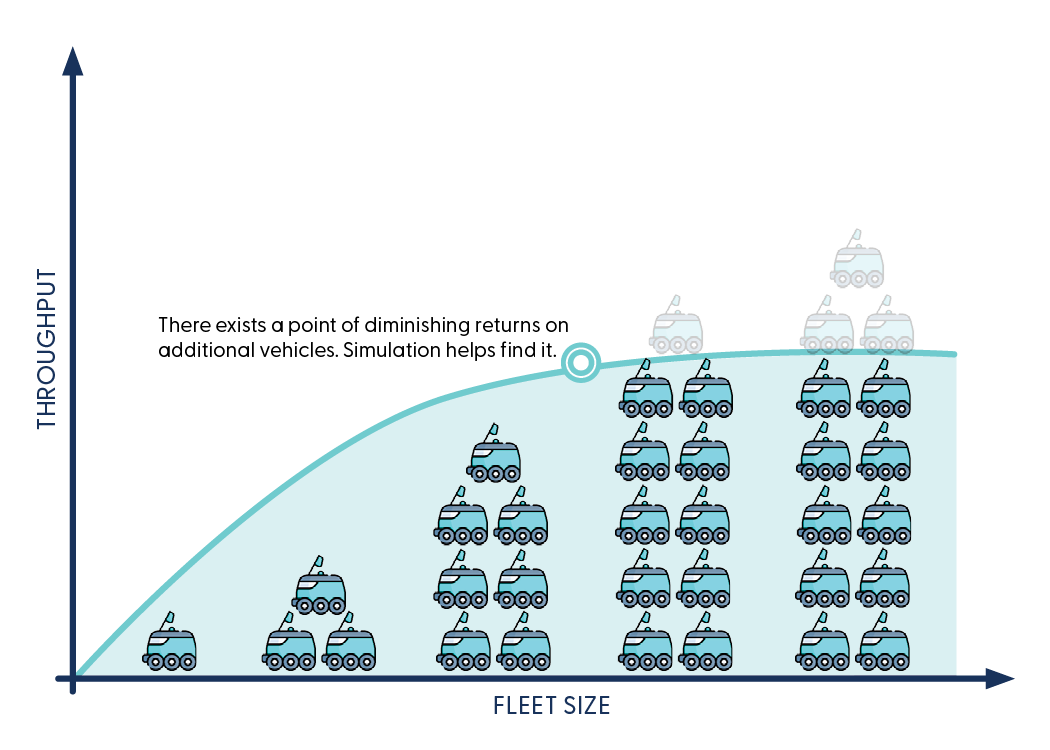
By understanding the thresholds of future growth that justify additional investments or system changes, businesses can proactively plan to keep operations running smoothly. Simulation thus provides a powerful tool for anticipating and mitigating potential challenges before they impact real-world performance.
4 Key Takeaways for Right-Sizing Your AGV Fleet
- Spreadsheets don’t tell the full story. Simulation is the most effective strategy to quantify fleet sizes for industrial autonomous vehicles.
- An ideal utilization is typically lower than you think. Natural ebbs and flows fluctuate the simultaneous needs for vehicles. Over-utilized fleets (even temporarily) can lead to destructive consequences on productivity.
- There’s no universal target utilization for AGVs. It really depends on each business’s cost of reduced throughput.
- Traffic is always a consideration. Sometimes improving the logic for assigning and routing autonomous vehicles can boost ROI with a lower fleet investment.
Conclusion
AMRs are a hot topic in industrial automation. If you’re considering a capital investment in autonomous vehicles, we can help optimize your investment and reduce risk of inefficient fleet size and design. Simulation is the most robust way to test how a complex system will perform. A thorough analysis of future scenarios will help uncover the right fleet sizes and help dial in important decision-making algorithms and travel paths so the project goes smoothly.
Headquarters
We have a team of engineers positioned across the US, but our primary HQ is in Atlanta, GA.