What are the Benefits of Virtual Commissioning?
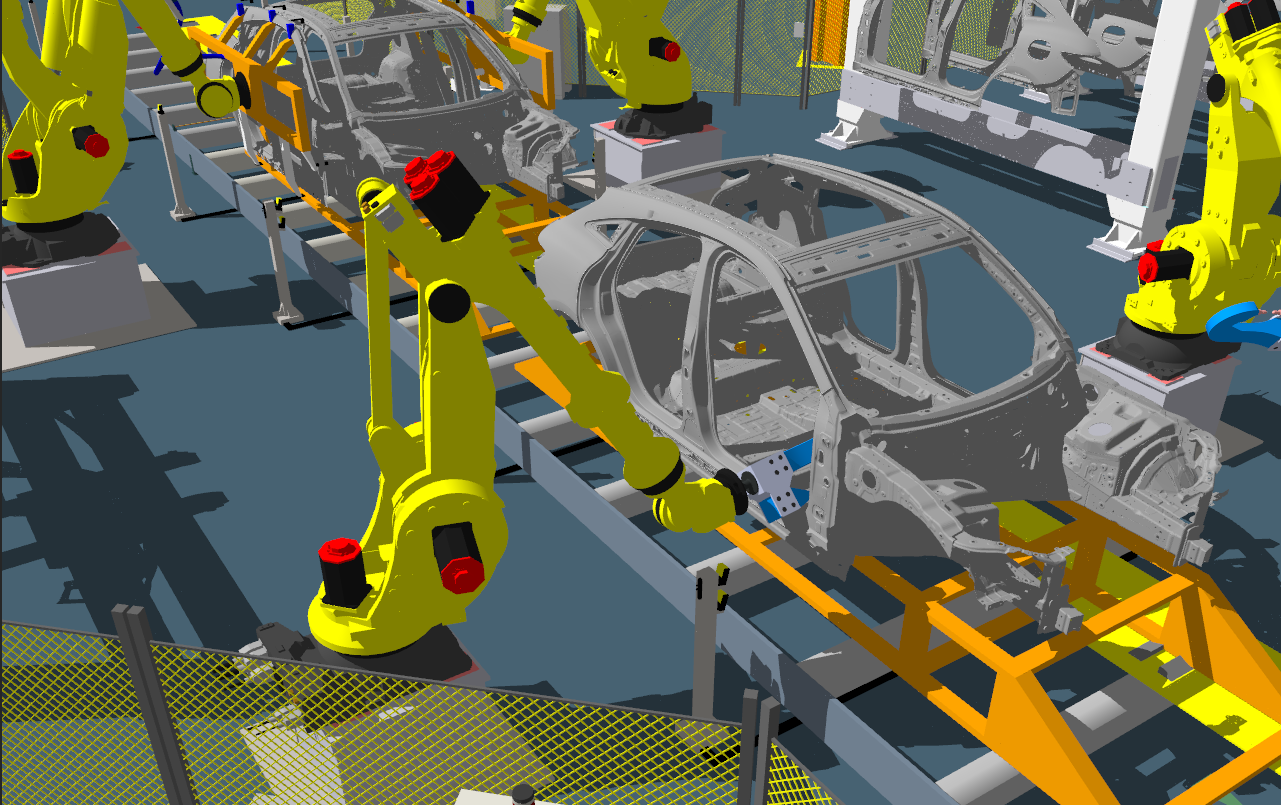
This is the first in a month-long series of posts we’ll be sharing on Virtual Commissioning. You can also download our free Virtual Commissioning Playbook here for more details on the process and benefits of VC.
As companies strive to maintain a competitive edge, traditional commissioning methods—where machinery and systems are set up and tested physically—are increasingly being complemented by virtual techniques.
Virtual commissioning (VC) is the practice of using a physics-based model to validate and fine tune the design, control logic, and performance of a system or machinery in a virtual environment. VC includes connecting the real-world control code (PLC, HMI, MES, robotics systems, etc.)to a virtual model – essentially tricking the controllers into thinking they’re running the real system. This process occurs before actual deployment on the factory or warehouse floor, allowing for early detection and resolution of potential issues.
By enabling detailed emulation and testing of systems before physical implementation, VC offers numerous benefits that significantly enhance efficiency and reduce risks, including:
Faster initial controls development and testing
Access to a VC environment allows controls engineers to develop their code with instant feedback. We can also validate, in real-time, the progress of controls development.
Anyone who has completed an industrial automation project in the past knows that controls are always the critical path. Without VC, controls engineers typically start their controls development process at power on. This is the last step and typically gets compressed introducing risk to the project schedule.
Faster start-up
By addressing controls code issues virtually, we remove a significant amount of time spent in the field (typically 50% or more).
Lower risk of impacting production time
Time is money when you have to shut down production during testing and validation on the factory floor. By utilizing VC, you can uncover and resolve hundreds of issues within your control systems ahead of time, with zero impact to production.
You never know what you might find
In-person FATs do not afford the same access as VC. With a physics-enabled, virtual model, we can test more scenarios in a faster and safer environment.
In rare occurrences, we find issues like mechanical interferences which require the design team to redesign part of the system. We hope this isn’t the case, but if it is, discovering those types of problems early on is considerably less expensive than finding out much closer to, or during, on-site commissioning.
Better trained site personnel
VC allows operators, maintenance, and site engineers to see how the equipment is supposed to operate weeks or months prior to go-live. This enables owners to learn how to operate the equipment in a realistic environment and how to handle situations when things go wrong.
Are you ready to implement VC for your operation?
To recap, VC minimizes costly downtime, accelerates project timelines, and ensures smoother integration of new systems into existing operations. As industries increasingly move towards digital transformation, adopting VC is becoming not just an option, but a strategic necessity to stay competitive.
Automation Intelligence has extensive experience performing VC projects for manufacturing and logistics clients across many different industries including automotive, consumer products, retail/eCommerce, and many others.
Headquarters
We have a team of engineers positioned across the US, but our primary HQ is in Atlanta, GA.